- 5005 Aluminum Block
- 5052 Aluminum Block
- 5083 Aluminum Block
- 5086 Aluminum Block
- 5182 Aluminum Block
- 5454 Aluminum Block
- 5754 Aluminum Block
- 6061 Aluminum Block
- 6063 Aluminum Block
- 6082 Aluminum Block
- 1060 Aluminum Block
- 2024 Aluminum Block
- 2A12 Aluminum Block
- 7005 Aluminum Block
- 7075 Aluminum Block
- 3003 Aluminum Block
NEWS
INFORMATIONTel:
86 17344894490aluminium block for milling
Last Updated :2023/06/13
Causes of Aluminium block for milling deformation
There are many reasons for the deformation of Aluminium block for milling, which are related to the material, part shape, and production conditions.
Aluminium block for milling mainly has the following aspects: deformation caused by internal stress in the blank, deformation caused by cutting force and cutting heat, deformation caused by clamping force.
Technological measures for reducing deformation of Aluminium block for milling
1 reduce the internal stress of the blank
Natural or artificial aging and vibration treatment can partially eliminate the internal stress of the blank. Pre-processing is also an effective process method. As for the blanks with big ears and large ears, because of the large margin, the deformation after processing is also large. If the excess part of the blank is processed in advance and the remaining amount of each part is reduced, not only the processing distortion in subsequent processes can be reduced, but also it can be released for a period of time after processing, and it can also release some of the internal stress.
2Improve the cutting ability of the tool
The material and geometric parameters of the tool have an important influence on the cutting force and cutting heat. Correct selection of the tool is very important to reduce the deformation of the part.
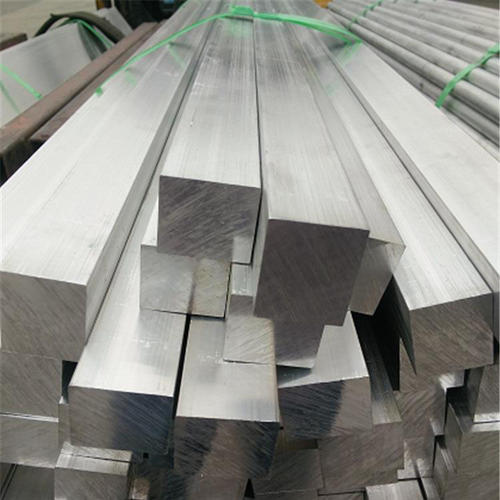
Operating techniques to reduce deformation of Aluminium block for milling
In addition to the reasons described above, Aluminium block for milling parts are deformed during processing. In actual operation, the operation method is also very important.
1. For parts with large machining allowances, in order to make them have better heat dissipation conditions during processing and avoid heat concentration, symmetrical processing should be used during processing. If a 90mm thick sheet needs to be machined to 60mm, if one side is milled immediately after the other side is milled, and the flatness is 5mm once; if repeated machining is used, each side is machined twice. The final size can guarantee flatness of 0.3mm.
2. If there are multiple cavities on the plate parts, it is not appropriate to use the sequential processing method of one cavity and one cavity during processing. This will easily cause uneven parts to be deformed.
3. Reduce cutting force and cutting heat by changing the amount of cutting. Among the three factors of cutting consumption, the amount of cutting back has a great effect on cutting force
There are many reasons for the deformation of Aluminium block for milling, which are related to the material, part shape, and production conditions.
Aluminium block for milling mainly has the following aspects: deformation caused by internal stress in the blank, deformation caused by cutting force and cutting heat, deformation caused by clamping force.
Technological measures for reducing deformation of Aluminium block for milling
1 reduce the internal stress of the blank
Natural or artificial aging and vibration treatment can partially eliminate the internal stress of the blank. Pre-processing is also an effective process method. As for the blanks with big ears and large ears, because of the large margin, the deformation after processing is also large. If the excess part of the blank is processed in advance and the remaining amount of each part is reduced, not only the processing distortion in subsequent processes can be reduced, but also it can be released for a period of time after processing, and it can also release some of the internal stress.
2Improve the cutting ability of the tool
The material and geometric parameters of the tool have an important influence on the cutting force and cutting heat. Correct selection of the tool is very important to reduce the deformation of the part.
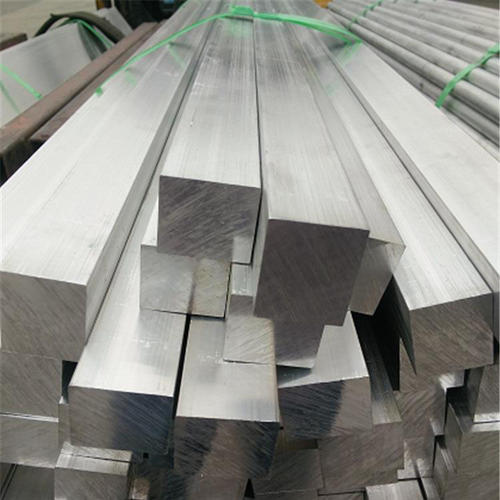
Operating techniques to reduce deformation of Aluminium block for milling
In addition to the reasons described above, Aluminium block for milling parts are deformed during processing. In actual operation, the operation method is also very important.
1. For parts with large machining allowances, in order to make them have better heat dissipation conditions during processing and avoid heat concentration, symmetrical processing should be used during processing. If a 90mm thick sheet needs to be machined to 60mm, if one side is milled immediately after the other side is milled, and the flatness is 5mm once; if repeated machining is used, each side is machined twice. The final size can guarantee flatness of 0.3mm.
2. If there are multiple cavities on the plate parts, it is not appropriate to use the sequential processing method of one cavity and one cavity during processing. This will easily cause uneven parts to be deformed.
3. Reduce cutting force and cutting heat by changing the amount of cutting. Among the three factors of cutting consumption, the amount of cutting back has a great effect on cutting force