- 5005 Aluminum Block
- 5052 Aluminum Block
- 5083 Aluminum Block
- 5086 Aluminum Block
- 5182 Aluminum Block
- 5454 Aluminum Block
- 5754 Aluminum Block
- 6061 Aluminum Block
- 6063 Aluminum Block
- 6082 Aluminum Block
- 1060 Aluminum Block
- 2024 Aluminum Block
- 2A12 Aluminum Block
- 7005 Aluminum Block
- 7075 Aluminum Block
- 3003 Aluminum Block
NEWS
INFORMATIONTel:
86 17344894490Is the engine cast iron or aluminum block better
Last Updated :2023/06/13
Which one is better, cast iron engine or aluminum block engine? Many people do not know, even some people do not know what is a cast iron engine, what is an aluminum block engine! Let's learn about it today!
I have deeply understood the advantages and disadvantages of cast iron cylinder blocks and aluminum alloy cylinder blocks. Let’s talk more today. First of all, the advantages and disadvantages of cast iron and aluminum alloy are very obvious, so everyone needs to use more rationality when looking at this issue. , because this is a balance between usage and product positioning. Let's talk about aluminum alloy first. The biggest advantage of aluminum is its low density and lighter weight compared to the same volume. However, some small-displacement engines have three cylinders in total. Can you say that it is for weight reduction?
I asked 20 people and they all told me that the aluminum-steel body is lighter, I asked what about the light? They said that this is a big trend. Except for the big trend, they can’t say anything. I think that in terms of small-displacement cylinder blocks, manufacturers who also use aluminum alloys generally have only one purpose, which is the product of the high-end engine module, which is used to balance The cost of large displacement, some models are after the high-end engine module, and the cost of the low-end three-cylinder and four-cylinder engines is shared. For example, someone asked me about iron ion or arc coating for aluminum engines a while ago. If it is worn out, can a steel sleeve be installed? I told him it was still not possible. Because the temperature feedback from the sleep to the oil passage loop of the thermal management of the cylinder is different, the signal feedback of the sensor may be messed up after the installation.
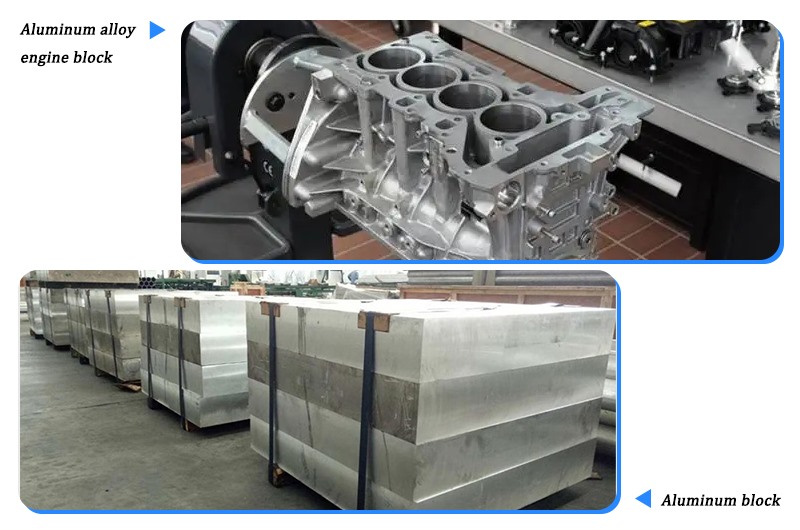
Everyone should know that the engine thermal management system is very expensive to design. If it is redesigned, it is basically equivalent to redesigning the engine. Therefore, it is unlikely for manufacturers to use aluminum for high-end engines and cast iron for low-end engines. It is to modularize the piston unit in one go, and evenly distribute the cost in materials and research and development. For example, BMW set the single-cylinder displacement at 500cc, because they found that this displacement can keep the acoustic vibration of the engine, work efficiency and mechanical friction. In a relatively good balance state, the displacement determines the cylinder bore and stroke of the piston, which is basically determined. The shape will change during combustion, but it is almost the same, and then a series of valve trains, pistons, tappet rockers, camshafts, etc. can all be similar.
In this way, the production process of these parts can be basically unified. Design drawings to make tools, machining, assembly costs, etc. can save money, naturally a lot of savings, but what is it in fact? Small-displacement engines must rely on the speed to increase to a certain extent, and the jitter will be reduced. For example, the idling speed of BMW's 15t3 cylinder is generally higher than that of Sigang, which is the way. What's more, many parts are preferentially designed for large-displacement engines under the same architecture. Compared with the average reciprocation times of the pistons of large-displacement and small-displacement engines, they have added a lot, and they have suffered a lot of loss in service life. Let's calculate the ratio and it will be clear.
Another point is the above-mentioned aluminum block engine. Cylinder liner is often used, especially the three-cylinder engine can't stand the archway of lightweight in terms of weight. What should the average car company do? Nowadays, many car companies will cancel the cylinder liner and use iron ion coating or arc spraying technology, but the durability of that thing is far from the iron cylinder liner. In normal use, even the iron ion coating is used. The steel of BMW n20b48 and Mercedes-Benz m282 may have the problem of partial wear of the cylinder coating during the warranty period. How wear-resistant is it?
For example, the Mercedes-Benz m282 engine has not yet appeared. After pulling it on the test bench and disassembling it to see the steel, the inner diameter of the cylinder is different everywhere, and in some places it is worn like a pig's large intestine. At this time, someone asked, will the large-displacement aluminum alloy cylinder block not be eccentric? First of all, you need to know that the technology used to locate higher-end large-displacement engines in the cylinder coating is different from the materials used in the province and small-displacement engines. In addition, large-displacement engines have less jitter and are under normal working conditions. The lower speed is also low, and the partial wear of the cylinder wall is naturally slow.
So it's still the same. These so-called advanced technologies are more compatible with large-displacement engines, and if they are placed on small-displacement engines, they are not troublesome for luxury brands. Here is my personal understanding. These car companies actually don’t want the engine to run another 1,2,3,000,000 kilometers. In that case, the update rate of the product will be reduced, preventing the vehicle from becoming a fast-moving consumer product. At the same time, the cost will be shared equally. Cutting the leeks of the working class to add to the large-displacement engines of the rich, so the durability of the vehicle is controlled within a certain range to increase market share.
To be honest, many first-tier luxury car companies have planned this way. If you don’t change cars, where will I get the profits? If you don't buy me a small displacement, where can I tilt a higher budget for a large displacement engine? right? There are other aluminum alloy cylinders that are easy to process. Some people dare to say this. Cans are easy to pinch.
Do you say that aluminum and steel are easy to process? Some people say that the official said so, is the manufacturer your father? What is said?
What are the facts like? in steel processing. Aluminum alloy materials will make the production line suffer more hidden losses. What is the hidden loss? The biggest difficulty in processing aluminum and steel is the lower tolerance of the expansion coefficient. The processing of aluminum and steel is very difficult, because the higher the expansion coefficient, the greater the deformation of the microscopic surface after the parts are heated, and the ductility of aluminum is also higher than that of aluminum. Cast iron is good. For example, the ability of drill bits to drill holes in cast iron cylinders is generally very strong, while the ductility of aluminum alloys is different from that of cast iron, and the ability to break wires is extremely poor Case.
Carbide drills that cannot be broken by iron wires may be broken, and this drill is a few hundred cheap and a few thousand expensive. There are dozens of holes in the steel body, which is a lot of money. So so. In terms of machining, if you can't solve this problem, you basically don't play. Now, in the tool industry, manufacturers have to reduce costs, and the yield rate is high. How many companies will be killed by this difficult material, what? Sandvik, the first-line tool manufacturers in Kennewalt, are now processed by the aluminum cylinder block and cylinder head, only they know.
I have deeply understood the advantages and disadvantages of cast iron cylinder blocks and aluminum alloy cylinder blocks. Let’s talk more today. First of all, the advantages and disadvantages of cast iron and aluminum alloy are very obvious, so everyone needs to use more rationality when looking at this issue. , because this is a balance between usage and product positioning. Let's talk about aluminum alloy first. The biggest advantage of aluminum is its low density and lighter weight compared to the same volume. However, some small-displacement engines have three cylinders in total. Can you say that it is for weight reduction?
I asked 20 people and they all told me that the aluminum-steel body is lighter, I asked what about the light? They said that this is a big trend. Except for the big trend, they can’t say anything. I think that in terms of small-displacement cylinder blocks, manufacturers who also use aluminum alloys generally have only one purpose, which is the product of the high-end engine module, which is used to balance The cost of large displacement, some models are after the high-end engine module, and the cost of the low-end three-cylinder and four-cylinder engines is shared. For example, someone asked me about iron ion or arc coating for aluminum engines a while ago. If it is worn out, can a steel sleeve be installed? I told him it was still not possible. Because the temperature feedback from the sleep to the oil passage loop of the thermal management of the cylinder is different, the signal feedback of the sensor may be messed up after the installation.
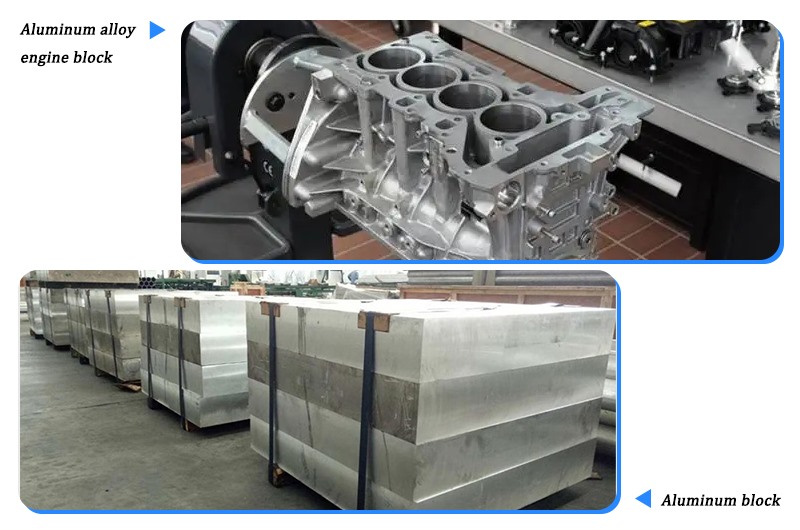
Everyone should know that the engine thermal management system is very expensive to design. If it is redesigned, it is basically equivalent to redesigning the engine. Therefore, it is unlikely for manufacturers to use aluminum for high-end engines and cast iron for low-end engines. It is to modularize the piston unit in one go, and evenly distribute the cost in materials and research and development. For example, BMW set the single-cylinder displacement at 500cc, because they found that this displacement can keep the acoustic vibration of the engine, work efficiency and mechanical friction. In a relatively good balance state, the displacement determines the cylinder bore and stroke of the piston, which is basically determined. The shape will change during combustion, but it is almost the same, and then a series of valve trains, pistons, tappet rockers, camshafts, etc. can all be similar.
In this way, the production process of these parts can be basically unified. Design drawings to make tools, machining, assembly costs, etc. can save money, naturally a lot of savings, but what is it in fact? Small-displacement engines must rely on the speed to increase to a certain extent, and the jitter will be reduced. For example, the idling speed of BMW's 15t3 cylinder is generally higher than that of Sigang, which is the way. What's more, many parts are preferentially designed for large-displacement engines under the same architecture. Compared with the average reciprocation times of the pistons of large-displacement and small-displacement engines, they have added a lot, and they have suffered a lot of loss in service life. Let's calculate the ratio and it will be clear.
Another point is the above-mentioned aluminum block engine. Cylinder liner is often used, especially the three-cylinder engine can't stand the archway of lightweight in terms of weight. What should the average car company do? Nowadays, many car companies will cancel the cylinder liner and use iron ion coating or arc spraying technology, but the durability of that thing is far from the iron cylinder liner. In normal use, even the iron ion coating is used. The steel of BMW n20b48 and Mercedes-Benz m282 may have the problem of partial wear of the cylinder coating during the warranty period. How wear-resistant is it?
For example, the Mercedes-Benz m282 engine has not yet appeared. After pulling it on the test bench and disassembling it to see the steel, the inner diameter of the cylinder is different everywhere, and in some places it is worn like a pig's large intestine. At this time, someone asked, will the large-displacement aluminum alloy cylinder block not be eccentric? First of all, you need to know that the technology used to locate higher-end large-displacement engines in the cylinder coating is different from the materials used in the province and small-displacement engines. In addition, large-displacement engines have less jitter and are under normal working conditions. The lower speed is also low, and the partial wear of the cylinder wall is naturally slow.
So it's still the same. These so-called advanced technologies are more compatible with large-displacement engines, and if they are placed on small-displacement engines, they are not troublesome for luxury brands. Here is my personal understanding. These car companies actually don’t want the engine to run another 1,2,3,000,000 kilometers. In that case, the update rate of the product will be reduced, preventing the vehicle from becoming a fast-moving consumer product. At the same time, the cost will be shared equally. Cutting the leeks of the working class to add to the large-displacement engines of the rich, so the durability of the vehicle is controlled within a certain range to increase market share.
To be honest, many first-tier luxury car companies have planned this way. If you don’t change cars, where will I get the profits? If you don't buy me a small displacement, where can I tilt a higher budget for a large displacement engine? right? There are other aluminum alloy cylinders that are easy to process. Some people dare to say this. Cans are easy to pinch.
Do you say that aluminum and steel are easy to process? Some people say that the official said so, is the manufacturer your father? What is said?
What are the facts like? in steel processing. Aluminum alloy materials will make the production line suffer more hidden losses. What is the hidden loss? The biggest difficulty in processing aluminum and steel is the lower tolerance of the expansion coefficient. The processing of aluminum and steel is very difficult, because the higher the expansion coefficient, the greater the deformation of the microscopic surface after the parts are heated, and the ductility of aluminum is also higher than that of aluminum. Cast iron is good. For example, the ability of drill bits to drill holes in cast iron cylinders is generally very strong, while the ductility of aluminum alloys is different from that of cast iron, and the ability to break wires is extremely poor Case.
Carbide drills that cannot be broken by iron wires may be broken, and this drill is a few hundred cheap and a few thousand expensive. There are dozens of holes in the steel body, which is a lot of money. So so. In terms of machining, if you can't solve this problem, you basically don't play. Now, in the tool industry, manufacturers have to reduce costs, and the yield rate is high. How many companies will be killed by this difficult material, what? Sandvik, the first-line tool manufacturers in Kennewalt, are now processed by the aluminum cylinder block and cylinder head, only they know.